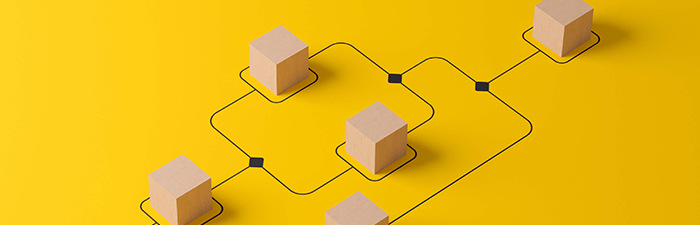
Part of defining a quality management process and determining quality metrics includes getting your company on the same page with terms. Two processes that can be confusing because, well, they both start with "quality" are Quality Assurance (QA) and Quality Control (QC). By understanding the differences between these two processes, you'll be closer to consistently delivering high quality products.
"Quality is not an act, it is a habit." - Aristotle
Quality Assurance ensures a product meets the required quality standards during product development. The goal of QA is to prevent defects and problems from being experienced by customers.
Quality Control is the process of finding defects and issues in the products after they have been manufactured or after they've been delivered to market. QC involves implementing inspection, testing, and building action plans to address identified issues.
The Importance of Clarification
There is no shortage of processes that share similar names, so definition becomes important. Setting the right definitions for your quality management processes has its benefits outside of clearing up some confusion. Here is a list of reasons why it's important to understand these two quality processes:
- Understanding the right approach to each process: QA and QC are two distinct approaches to quality management, and understanding the difference between them is essential to know when to use each approach appropriately. Organizations need to know when to use each process to effectively manage quality, reduce defects and issues, and meet customer expectations.
- Building an effective quality management strategy: Developing a good quality management strategy requires an approach that considers the unique needs and requirements of an organization at different points in the product lifecycle.
- Improving product quality: Implementing effective quality processes can help organizations reduces product bugs and defects which improves product quality, and ultimately increase customer satisfaction.
- Meeting industry standards: Many industries have specific regulatory and industry standards that organizations must comply with to ensure the quality and safety of their products or services.
- Ensuring effective communication: By understanding the roles and responsibilities of different teams in the quality management process, organizations can ensure that everyone is working towards the same quality goals and objectives.
What's the difference between quality assurance and quality control?
While the two terms are sometimes used interchangeably, there are a few key differences to help better understand when and how they can be used to create high quality products.
Purpose
The purpose of QA is to prevent defects and errors from occurring by identifying and addressing potential issues before they cause damage. QC's purpose is to detect and correct defects and errors after they have occurred.
Focus
QA is concerned with the entire process of product or service development, from design and development to delivery to the customer. It focuses on improving processes and preventing defects and errors from occurring. While, QC is focused on the final output of the product or service development process. It focuses on detecting and correcting defects and errors in the finished product or service.
Approach
QA is a proactive approach to quality management that involves identifying potential issues, implementing quality planning and control measures, and continuously monitoring and improving the quality of the product or service. QC is a reactive approach that involves implementing inspection and testing processes, analyzing data, and developing corrective and preventive action plans.
Responsibility
Quality is a collaborative effort that involves everyone from top management to front-line employees to ensuring the quality of the product or solution. Both QA and QC responsibilities are typically assigned to a specific department or team, such as the quality control, software quality assurance, or test engineering departments.
Goal
The goal of QA is to prevent defects and errors from occurring in the first place by improving processes and implementing quality planning and control measures. The goal of QC is to find and correct defects and errors in the finished product or service.
The Similarities Between QA and QC
The similarities between these two processes tend to be what causes the confusion or misunderstanding of what each of them do. Here are four similarities between QA and QC:
- Quality is the key - Both processes are essential for managing quality and meeting customer expectations.
- Data drives their decisions - They rely on data, such as inspection results, statistical analysis, and customer feedback, to identify opportunities for improvement and measure the effectiveness of quality management processes.
- Require collaboration between teams- Collaboration between different departments and teams within an organization is required. For example, in QA, everyone in the organization is responsible for ensuring the quality of the product or service, while in QC, the responsibility for ensuring quality is typically assigned to a specific department or team.
- Tuned into continuously improving - By monitoring and measuring the effectiveness of quality management processes and implementing corrective and preventive action plans, organizations can continuously improve the quality of their products or services.
When to Use QA vs. QC
One of the easier ways to spot the differences between these two processes is to determine when they are happening in the software development lifecycle. QA tends to happen during the design, development, and launch of a product while QC tends to be out of the manufacturer or after a product is released. Here are more details about when to use each process:
When to Use Quality Assurance
Being proactive QA concerns itself with the entire process of product or service development, from design and development to delivery to the customer.
- During the Design and Development Phase
- When Implementing Process Improvements
- When Building Trust with Customers
When to Use Quality Control
The reactive approach to QC concerns itself with the final output of the product or service development process.
- During the Manufacturing Phase
- When Responding to Customer Complaints
- When Monitoring and Controlling Processes
Implementing Effective QA and QC Processes
Implementing effective Quality Assurance and Quality Control processes is critical for managing quality and ensuring customer satisfaction. Here are some key factors to consider when implementing effective QA and QC processes:
Identifying Key Quality Metrics
- To effectively manage quality, organizations need to identify key quality metrics that they will use to measure the effectiveness of their QA and QC processes. Some common quality metrics include defect rates, customer satisfaction ratings, and product reliability measures.
Developing Quality Planning and Control Measures
- Implementing quality planning and control measures to prevent defects and errors from occurring. This can include developing product design guidelines, establishing quality control procedures, and implementing process improvement initiatives.
Implementing Inspection and Testing Processes
- By setting up inspection and testing processes, organizations can ensure that their products or services meet the required quality standards and meet or exceed customer expectations.
Developing Corrective and Preventive Action Plans
- When defects or errors occur, organizations need to develop corrective and preventive action plans to address the issue and prevent it from happening again. This can involve root cause analysis, developing corrective action plans, and implementing preventive measures.
Key Takeaways
Quality Assurance and Quality Control are important quality management process that serve different purposes and use different approaches. Understanding the differences between QA and QC is useful for effectively managing quality, meeting customer expectations, complying with industry standards and regulations, and ultimately improving the quality of products.
To implement effective QA and QC processes, organizations should identify key quality metrics, develop quality planning and control measures, implement inspection and testing processes, and develop corrective and preventive action plans.
By focusing on these factors and understanding the similarities and differences between QA and QC, organizations can develop a comprehensive quality management strategy that leverages the strengths of both approaches. Ultimately, effective QA and QC processes can help organizations manage quality, reduce defects and errors, and meet or exceed customer expectations, even in challenging circumstances.